脱硫技术简明介绍及腐蚀防护要点手册
艾柯尔橡胶防腐(武汉)有限公司----张欣
第一篇
脱硫工艺介绍
我国是世界上最大的煤炭生产和消费国,煤炭在中国能源结构中的比例高达76.2%,我国排放的SO2 90%均来自于燃煤。近几年,我国虽然采取了排污收费政策,但每年的SO2排放量仍超过2000万吨,酸雨污染面积迅速扩大,对我国农作物、森林和人体健康等方面造成巨大损害,也成为制约我国经济、社会可持续发展的重要因素,因此,对SO2排放的控制已势在必行。
对于SO2排放的控制,除了限制高硫煤的开采和使用、调整能源结构以外,重点治理的是火电厂的SO2污染。按我国电力行业的发展规划,2000年至2010年十年中,火电装机容量将增加1.5亿kW,且国家规定控制区内新建、改造火电厂,必须建设脱硫设施。因此,未来十几年,我国脱硫市场十分巨大。
烟气脱硫是目前世界上唯一大规模商业化应用的脱硫方式,是控制二氧化硫污染的主要技术手段。国外烟气脱硫技术研究始于十九世纪五十年代,目前已有数千套烟气脱硫装置投入运行。在成功地控制了二氧化硫污染的同时,各发达国家已形成烟气脱硫相关环保产业。我国自60年代就开始了零星的烟气脱硫研究,80年代后期开始列为重点课题,但由于燃煤这部分烟气流量大,SO2浓度低,技术难度较大,到目前为止,较大机组的国产化脱硫设备仍无较大突破。目前,利用与国外的合作,对技术和部分设备的引进,建成了多座具有工业规模、行之有效的脱硫示范装置,为我国脱硫市场的快速发展奠定了基础。按照环保发展和我国经济实力的要求,我国必须加快脱硫技术和设备的国产化和产业化,要加快对引进脱硫技术的引进、消化、吸收工作。
烟气脱硫技术主要利用各种碱性的吸收剂或吸附剂捕集烟气中的二氧化硫将之转化为较为稳定且易机械分离的硫化合物或单质硫,从而达到脱硫的目的。FGD的方法按吸收剂和脱硫产物含水量的多少可分为两类:(1)湿法,即采用液体吸收剂洗涤以除去二氧化硫。(2)干法,用粉状或粒状吸收剂、吸附剂或催化剂以除去二氧化硫。按脱硫产物是否回用可分为回收法和抛弃法。按照吸收二氧化硫后吸收剂的处理方式可分为再生法和非再生法(抛弃法)。
简易湿式石灰石/石膏工艺法
是降低排放标准或简化部分设备的脱硫方法,该工艺的优势是系统较简单,造价低,运行费用低,太原电厂采用了该方法。根据目前我国一些电厂机组容量较小或燃煤含硫量不是太高的情况,采用简易脱硫法是可能的。
氨-肥法脱硫技术
氨法是用氨水洗涤含SO2的废气,形成(NH4)2SO3-NH4HSO3-H2O的吸收液体系。该溶液中(NH4)2SO3对SO2具有很好的吸收能力,是氨法中的主要吸收剂。
氨法是烟气脱硫方法中较为成熟的方法,较早的被应用于工业工程。该法脱硫费用低,氨可留在产品内,以氮肥的形式提供使用,因而产品使用价值较高,但氨的来源受地域及生产行业的限制较大。尽管如此,氨法仍不失为一个治理低浓度SO2的有前途的方法。
该技术是由华东理工大学肖文德博士发明的。它是以氨为脱硫剂,对烟气中二氧化硫进行脱硫后经特殊工艺生成硫酸铵肥料的一种脱硫工艺。该技术不仅拥有完整的自主知识产权,同时副产品为化肥,不存在二次污染,投资省,运行成本低,技术性和经济性非常高,市场前景广阔。
远达公司与华东理工大学共同向国家科技部申报NADS氨-肥法脱硫技术“863”项目,在竞争中已获得批准,并获取国家科技部补助资金500万元。目前,远达公司、华东理工大学和肖文德博士三方已成立合资公司“上海益科科技有限公司”,向全国推广氨-肥法脱硫技术。
工作原理:工艺过程主要由吸附、萃取、中和、吸收、氧化、浓缩干燥等单元操作组成 。
第一级脱硫:
SO2被活性炭吸附催化氧化成SO3 ,饱和的活性炭洗涤再生即能得到稀硫酸:
SO2 +O2+H2O→H2SO4
稀硫酸与磷矿粉发生反应, 萃取过滤后可获得磷酸:Ca10(PO4)6F2+10H2SO4+20H2O→6H3PO4+2HF+10CaSO4·2H2O
第二级脱硫:
用氨中和磷酸制脱硫吸收液:
H3PO4+NH3→NH4H2PO4(磷酸二氢銨)+NH3→ NH4H2PO4(磷酸氢二銨)
SO2的二级吸附反应:
(NH4)2HPO4+SO2+H2O→(NH4)H2PO4+NH4HSO3
2(NH4)2HPO4+SO2+H2O→2NH4H2PO4+(NH4) 2SO3
NH4H2PO4+NH3→(NH4)2HPO4
在脱硫过程中,需不断向循环液补充氨, 最后将脱硫肥料浆氧化及浓缩干燥,并对受热不稳定的(NH4)2SO3进行氧化处理:
2(NH4)H2PO4+(NH4)2SO3+1/2O2→ 2NH4H2PO4+ (NH4)2SO4
氧化后的脱硫液,通过蒸发浓缩干燥,即制得固体肥料。
湿式石灰石-石膏法
该法用石灰或石灰石的浆液吸收烟气中的SO2,生成半水亚硫酸钙或石膏。其技术成熟程度高,脱硫效率稳定,可达90%以上。目前是国外工业化烟气脱硫的主要方法SO2。
石灰-石膏法是采用石灰石或石灰的浆液吸收烟气中的SO2,属于湿式洗涤法,该法的副产品是石膏(CaSO4·2H2O)。在主吸收塔内完成SO2的吸收和氧化两个步骤,分别在吸收塔和塔釜内完成。
原理: 中和生成H2O,使得上述平衡向右进行。水中溶解的石灰石离解产生OH-离子,将反应产生的H

(1) 吸收 |
(2) 氧化 |
CaO+H2O→Ca(OH)2 |
2 CaSO3·1/2H2O+O2+3H2O→2 CaSO4·2H2O |
Ca(OH)2+SO2→CaSO3·1/2H2O+1/2H2O |
Ca(HSO3)2+1/2O2+H2O→CaSO4·2H2O+SO2↑ |
CaCO3+SO2+1/2H2O→CaSO3·1/2H2O+CO2↑ |
|
CaSO3·1/2H2O+SO2+1/2H2O→Ca(HSO3)2 |
|
鼓入的空气可将生成的CO2带走,也可用来氧化在上述有关反应中得到的HSO3-和SO32-离子。最后生成石膏沉淀物。
烟道气的脱硫处理采用廉价的石灰(生石灰或熟石灰)作为反应物。高温烟气从吸收塔底部进入,按要求配置的循环液,由吸收塔顶部喷淋,烟气在上升过程中与循环液充分接触,发生化学反应,使烟气中的SO2被吸收。净化后的烟道气通过除雾器去除水雾后进入烟道,达标排放,全过程实现自动控制,并可在线监测SO2浓度。
为防止亚硫酸钙分解出SO2,同时减少亚硫酸钙结晶可能对喷淋系统造成的影响,在循环液中进行曝气,将亚硫酸钙氧化为硫酸钙,固液分离后,外排最终处置或综合利用。
整个烟气脱硫系统主要由石灰乳制备、烟气预处理、循环吸收系统、烟气再热和控制系统五个子系统组成。
1、石灰乳制备系统
石灰以石灰粉的形式运送到厂,存放于石灰贮罐内,系统运行时,石灰贮罐中的石灰粉经石灰给料机送至熟化槽中,加水熟化,并加以搅拌,配置成浓度较高的石灰浆液,然后进入陪送槽加水搅拌,稀释成吸收液,再由石灰乳泵送至循环槽。
2、烟气预处理系统
在烟气预处理器中,由预循环泵抽取循环槽内的吸收液对烟气进行喷淋洗涤,洗涤后的浆液进入灰渣槽沉淀,上清液回到循环槽。洗涤后的烟气进入脱硫塔。
3、循环吸收系统
烟气从脱硫塔的底部进入,由循环泵抽取循环槽中的吸收液从脱硫塔顶部经喷淋系统以雾状喷下,在吸收塔内部形成吸收液雾滴与烟气的交汇区域,完成二氧化硫的脱除过程。反应后的烟气经过除雾器除去水雾,从底部排出。反应后的液体进入吸收塔下面的循环槽,循环槽为钢筋混凝土结构,用于贮存吸收液。循环槽底部设曝气装置,由鼓风机鼓风曝气,将不稳定的亚硫酸钙转化为稳定的硫酸钙。底部浓度较大的渣浆送至渣浆处处理系统,上部吸收液与不断补充进来的新配吸收液一起循环使用。
渣浆泵将循环槽底部浓度较大的渣浆抽入灰水分离器,由灰水分离器将石膏和水分离,水进入回用水池,用作配置吸收液,石膏由皮带输送机送至石膏堆放场。
4、烟气再热系统
进入烟气预处理器前的高温烟气由换热风机送至脱硫塔出口的烟气再热器,在烟气在热气中经过热交换,使脱硫后的烟气温度升高,以避免在烟囱内结露和保证烟气的抬升高度。
5、控制系统
■ 适用范围
■ 技术特点
■ 投资省
■ 脱硫效率高
■ 先进的控制技术,实现全过程自动控制
■ 很好地解决设备结垢问题和吸收塔及内部组件的腐蚀问题
■ 可按照用户要求设计
■ 技术参数
脱硫效率:85%~95%
设计液气比(L/M3):2~4:1
钙硫比:1.1:1
整个脱硫系统阻力小于1000Pa;
烟气含湿量:<8%
PH在7.6-8.2之间
浆液浓度:12%
吸收剂(石灰粉)细度:>200目,纯度:>90%
两级折板式除雾器,阻力为450Pa
吨锅炉投资:3-4万元;
每KW脱硫投资:150-200元;
运行费用:小于700元/吨二氧化硫,平均每度电增加成本 3分
在吸收液中加入有机添加剂,防止设备的结垢。
该法终产物为石膏。简易石灰石/石膏法对终产物不加回收,直接抛弃;亦可采用后处理分离出成品石膏回收利用。
湿式烟气脱硫除尘一体化工艺
是本公司针对旋流板塔所特有的优良性能,结合国内企业的实际情况,而设计的一种高效、经济的FGD工艺。除尘效率≥98%,脱硫率75%~90%,满足国内现行的治理要求;特殊设计组合式除雾装置防止风机带水。
该法一般使用石灰为吸收剂,或用电石渣及其它碱性废渣。反应原理如下:
CaO+H2O→Ca(OH)2
Ca(OH)2+SO2→CaSO3·1/2H2O+1/2H2O
CaCO3+SO2+1/2H2O→CaSO3·1/2H2O+CO2↑
CaSO3·1/2H2O+SO2+1/2H2O→Ca(HSO3)2
脱硫液经综合循环池沉灰、补充碱后循环使用。
该法所得副产品可以回收,也可以抛弃。石灰石料源广泛,原料易得,且价格低廉,治理效果好,在国内多家企业均有成功实施的业绩。
烟气循环流化床干法脱硫装置 1、工艺流程
烟气循环流化床干法脱硫工艺流程如下图所示,此脱硫装置利用消石灰(Ca(OH)2)作为吸收剂,吸收并除去烟气中的SO2,SO3、HF、HCl等有害气体及重金属微粒。
未经处理的烟气从吸收塔(即流化床)底部进入。吸收塔底部为一个文丘里装置,烟气流经文丘里管后速度加快,并在此与很细的吸收剂粉末互相混合,颗粒之间、气体与颗粒之间剧烈摩擦,形成流化床,在喷入均匀水雾调质下,吸收剂与烟气中的SO2反应生成CaSO3和CaSO4。脱硫后携带大量固体颗粒的烟气从吸收塔顶部排出,先进入机械预除尘器,大部分烟气中的固体颗粒都被分离出来,被分离出来的颗粒经中间灰仓循环返回吸收塔,由于固体颗粒反复循环达百次之多,故吸收剂利用率较高。
从机械预除尘器排出的烟气经除尘器进一步除尘后,由引风机排入烟囱。
该脱硫工艺所产生的副产物呈干粉状,其化学成分主要由飞灰、CaSO3、CaSO4和未反应完的吸收剂Ca(OH)2等组成,适合用于填埋、筑路、水泥添加剂等。
2、系统组成
烟气循环流化床脱硫系统由吸收剂制备系统、吸收塔系统、脱硫灰再循环系统、除尘器及控制系统等部分组成。
3、技术特点
(1)系统简单、运行可靠、操作方便,适合于300MW及以下机组的烟气脱硫;
(2)占地面积小、投资低,不仅适合于新建电厂的SO2治理,也适合于老电厂的改造;
(3)由于吸收剂的循环使用,反应停留时间长,脱硫效率高(最高可达99%);
(4)采用清洁烟气再循环,可适合锅炉运行负荷40%~110%的变化;
(5)净烟气无须再热,可直接排空;
(6)脱硫副产物呈干粉状,适合于填埋、筑路和水泥添加剂等,对环境不会造成二次污染。
双碱法
该工艺先用可溶性的钠碱吸收液在吸收塔内进行脱硫,然后在塔外再用石灰乳或石灰石浆液对吸收液进行再生和分离,再生液继续进行循环脱硫。
钠钙双碱法有如下优点:塔内钠基清液作为吸收液,大大降低了结垢机率;钠基吸收二氧化硫速率高,在较低的液气比下可得到较高的脱硫率,同时还可大大提高石灰的利用率。
循环过程中的主要反应如下:
(1)脱硫过程 |
(2)再生过程(用石灰乳) |
Na2CO3+SO2→Na2SO3+CO2↑ |
2NaHSO3+Ca(OH)2→Na2SO3+CaSO3+H2O |
2NaOH+SO2→Na2SO3+H2O |
Na2SO3+Ca(OH)2→2NaOH+CaSO3 |
Na2SO3+SO2+H2O→2NaHSO3 |
|
亚钠法
该法是用碳酸钠碱溶液作吸收剂,SO2与碳酸钠作用生成亚硫酸钠和亚硫酸氢钠,属湿法脱硫,结垢几率小。该法脱硫效率可达90%以上,技术较成熟,也是目前国外工业化烟气脱硫的常用方法。
喷雾干燥法
该法是采用石灰乳为吸收剂的烟气脱硫法,属半干法脱硫,脱硫效率80%-90%,投资比湿式石灰石-石膏法低。目前在德国、奥地利、意大利、丹麦、瑞典等国应用较多。
吸收再生法
主要有氧化镁法、双碱法、W-L法。脱硫效率可达95%左右,技术较成熟。
脉冲电晕等离子体降解有机废气
随着工业的发展,有机废气的排放量迅速增加,其治理问题日益为人们所重视。有机废气种类多,往往组成复杂、浓度呈无规律的变化,这就给治理带来了难度。目前国内外采用的处理方法中,催化燃烧法因其净化效率高,工艺简单,是应用最广的一种,也有不少国产装置;但其主要问题是能耗大,尤其是废气浓度低时热回收量少能耗更大;又浓度变化大时适应性不佳等亦限制了其应用。因而,工程实际使用率并不高。吸附法可回收溶剂,但缺点是吸附剂的容量有限而设备庞大,吸附剂再生及溶剂回收等后处理工程复杂。其它的治理方法如冷凝法、吸收法等应用范围更为有限。因此,经济、高效的治理低浓度有机废气,除改进传统技术外,尚需开发新的技术。
基于这一背景,浙江大学在谭天恩教授领导的科研小组93年起开展了脉冲电晕放电下去除有机物的研究。于95年申请国家自然科学基金并获得资助,至今已发表了30多篇科学论文,在理论和实验上作了系统地研究。脉冲电晕等离子体脱除有机物的基本原理是通过前沿陡峭、脉宽窄(纳秒级)的高压脉冲放电,在常温常压下获得等离子体,其中的高能电子和O×、OH×等活性粒子与有机物进行氧化、降解反应,使污染物转变为无害物。
有机物热力燃烧起燃的温度在700°C以上,催化燃烧也需高于200°C,而在等离子体内催化降解有机物可在常温常压下进行。本技术就是巧妙地利用了等离子体与催化反应的协同效应提高有机废气净化率、降低能耗,为开发经济有效的有机废气治理方法,特别是现有技术难以处理的低浓度、大流量有机废气,开拓了新途径。其潜在的社会和经济效益都是巨大的,应用前景广阔。
炉内喷钙-增湿活化脱硫法
该法是一种将粘状钙质吸收剂(石灰石或石灰)直接喷入燃烧燃油锅炉炉膛的脱硫技术,主要适用于中、低硫煤燃油锅炉,脱硫效率可达80%。
旋流板塔工作原理
旋流板塔工作时,烟气由塔底从切向高速进入,在塔板叶片的导向作用下旋转上升。逐板下流的液体在塔板上被烟气喷成雾滴状,使气液间有很大的接触面积。液滴在气流的带动下旋转,产生的离心力强化气液间的接触,最后被甩到塔壁上,沿壁下流,经过溢流装置流到下一层塔板上,再次被气流雾化而进行气液接触。由于塔内提供了良好的气液接触条件,气体中的SO2等酸性气体被碱性液体吸收的效果好;旋流板塔同时具有很好的除尘性能,气体中的尘粒在旋流塔板上被水雾粘附,并受离心力作用甩到塔壁而除去,从而具有较高的除尘除雾效率。本公司设计的特殊组合式除雾装置,将进一步保证高效的除雾性能,以避免风机带水问题。
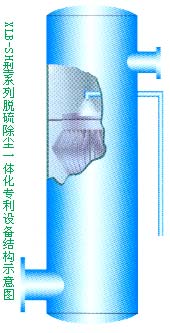
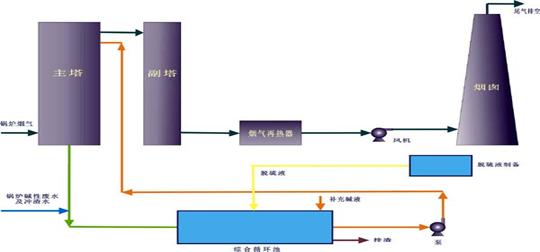
旋流板塔湿法脱硫反应原理
湿法烟气脱硫是应用最为广泛的脱硫技术,湿法烟气脱硫的基本过程是用含脱硫剂的溶液或浆液在旋流塔板中洗涤烟气,使烟气中的二氧化硫在旋流板塔内较好传质条件下,与脱硫液进行较为充分的吸收反应,从而大大降低烟气中的二氧化硫浓度,达到脱硫目的。湿法烟气脱硫可以达到较高的脱硫效率,工程投资和运行费用都较低,管理和维护也较为方便。湿法脱硫的主要缺点是净化烟气的温度较低,应进行净化烟气的再加热,以防露点腐蚀并有利于烟气排放后的烟气抬升。
石灰石是最早作为烟气脱硫的吸收剂之一,由于石灰和石灰石的价格低廉、取料广泛,使得石灰/石灰石法的运行费用在各种脱硫方法中相对低而应用最广泛。石灰/石灰石浆液在旋流板塔中洗涤烟气的总的反应是SO2和Ca(OH)2或CaCO3起作用,生成亚硫酸钙,其一部分氧化成硫酸钙。为了进一步的脱硫渣的处理,我们采用强制氧化生产石膏的工艺。
双碱法烟气脱硫技术早已在日本和美国的大型工业装置上成功应用。该法流程特点为先用可溶性的钠碱吸收液在吸收塔内进行脱硫,然后在塔外再用石灰乳或石灰石粉对钠基吸收液进行再生,在我们的工艺中电石渣常被用来替代石灰进行再生。再生液继续进行循环脱硫。双减法有如下优点:塔内钠基清液作为吸收液,大大降低了结垢机率;钠基吸收二氧化硫速率高,在较低的液气比下可得到较高的脱硫率,同时还可大大提高石灰的利用率。反应主要方程式如下:
吸收过程: Na2CO3 + SO2 → Na2SO3 + CO2↑
2NaOH + SO2→ Na2SO3 + H2O
Na2SO3 + SO2 + H2O → 2NaHSO3
再生过程: 2NaHSO3 + Ca(OH)2 → Na2SO3 + CaSO3 ↓+ 2H2O
Na2SO3 + Ca(OH)2 → 2NaOH + CaSO3↓
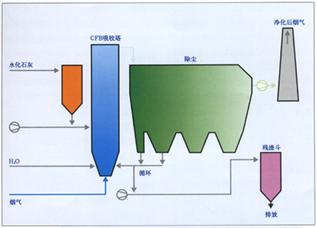
旋流板塔发展历程
旋流板塔是浙江大学谭天恩教授为首的研究小组开发的、曾获国家发明奖的一种高效通用型传质设备(专利号ZL94210374.2),具有气液通量大、压降低、操作弹性宽、除尘效率高、不易堵、效率稳定等优点,其综合性能优于目前国内外普遍使用的其它脱硫塔。
旋流板塔自1974年首次用于衢州化工公司碳铵干燥尾气回收氨以来,已广泛用作中小氮肥厂的半水煤气脱硫(H2S)塔、饱和热水塔,除尘、冷却、冷凝塔等,也用于环保行业脱除烟气和废气中的飞灰、SO2、NOx、H2S及铅、汞蒸汽等,取得了巨大的环境效益和社会效益,获得1978年全国科学大会奖和1984年国家发明奖。至90年代,在国家自然科学基金和省自然科学基金(各二次)的资助下,以谭天恩教授为首的研究小组又对旋流塔板上的气液运动、传质效率、放大效应等进行了深入的研究,又获得化工部1993年科技进步二等奖、国家教委1996年科技进步三等奖、1999年浙江省环境保护科技进步二等奖。
从80年代前期开始,旋流板塔开始用于小型锅炉的烟气脱硫研究,在实验室的基础上对同时脱硫、除尘、除雾相关的工程性问题进行了深入研究。旋流板塔石灰/石灰石法、以及双碱法、电石渣和废碱液脱硫技术作为实用可靠的脱硫除尘技术,具有投资和运行费用低、操作弹性大、管理和维护方便等特点,现已逐渐推广应用于电力、化工、矿冶、轻工等行业的烟气脱硫除尘和其它工业废气治理。在“九五”期间,浙江大学环境工程研究所承接了国家“九五”重点科技攻关项目,对旋流板塔脱流除尘一体化技术进行了工艺优化、设备结构优化、防腐耐磨材料、成套化、系列化等方面的研究在工业应用上获得了巨大的成功,并于2000年12月通过国家环保总局召开的国家“九五”重点科技攻关项目“旋流板塔湿法烟气脱硫除尘技术与装备研究”成果鉴定会,鉴定委员会一致认为: “该技术与装备达到国际先进水平,建议国家有关部门大力支持和加快该成果的推广和应用”。
循环流化床CFB工艺 烟气中酸性有害气体SO3,SO2,HCL和HF通过含 有细小颗粒的强化膨胀在循环流化床反应塔内的反应来去除。这些颗粒由吸收剂--Ca(HO)2、飞灰和脱硫反应物构成。从CFB吸收塔底部注入水,用以调节优化吸收条件。注水与吸收剂的添加是分开进行的。
海水脱硫 引进了鲁奇·比晓夫的海水脱硫工艺。对于那些在海边的电厂而言,海水脱硫工艺将是一个经济节省的选择。在海水脱硫装置中,碱性海水用来去除烟气中二氧化硫、氯化氢和氟化氢。溶解的硫离子被吸收成中性产物留在海水中。化学反应结束后,洗涤用水的硫酸根离子含量略为增加并被排入大海,对海洋环境不会造成大的影响。
海水脱硫化学原理示意图

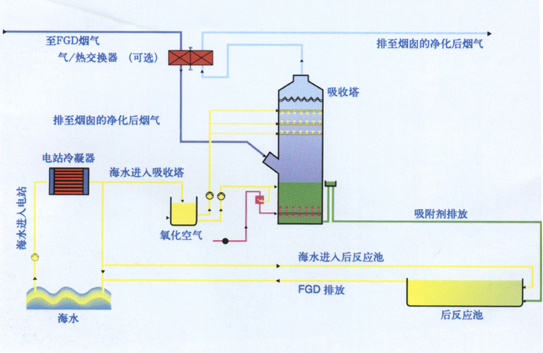
海水-白泥脱硫技术 是青岛四洲电力设备有限公司与青岛海洋大学合作开发,适用于沿海发电厂烟气脱硫。本技术具有自主知识产权和国际先进水平的新型脱硫技术,已通过鉴定和中试,获二项国家发明专利。该技术是在海水中添加适量碱厂废弃物(白泥)或就地取材的钙镁盐(如电厂泥、废灰、石灰石等)作为吸收剂,来脱除烟气中的二氧化硫,具有以废治废、双向治理、成本低、效率高、无淡水消耗与二次污染,并适用于中、高硫煤等优点。该技术将填补国内空白,可以完全替代进口,具有广阔的市场前景和巨大的经济效益。二、主要技术指标(以130t燃煤锅炉脱硫工程为例) 1.脱硫率>90% 脱硫率是指脱硫后与脱硫前烟气中二氧化硫浓度(mg/Nm3或ppm)之比。该技术指标能否达到要求是项目成功与否的关键,本项目所实施的脱硫技术,可以根据燃煤含硫量的不同改变海水—白泥乳浓度和气/液比值来达到所需脱硫率要求。故本脱硫技术不受发电厂不同燃煤含硫量的限制。 2.总体气/液比值(V/V)>120 总体气/液比值是指脱硫烟气量与所需脱硫剂(海水—白泥乳液)之体积比。 该技术指标的大小直接决定了整个脱硫系统的功耗和设备规格,从而进一步决定了系统占地面积、投资规模及运行费用等,是衡量脱硫系统经济性的重要技术指标。 3.曝气氧化过程中空气中氧的利用率6~8% 脱硫剂(海水—白泥乳液)吸收二氧化硫后,吸收塔流出液中含有亚硫酸(氢)根,必须将其氧化成硫酸根。在相同功率下曝气时,还原物的氧化速度和空气中氧的利用率是相关的两个工程指标,经室内模拟实验和实地脱硫试验表明,这两个指标除与曝气深度、分散状态、曝气量及布设位置等物理因素有关外,自生催化剂和调控pH至关重要,本项目技术正是在优化设计曝气装置的同时,更着重考虑了自生催化剂和pH对此化学动力过程的影响,使氧的利用率由单纯海水脱硫的2%提高到6~8%,从而降低了动力消耗,并较大幅度地缩减了曝气面积。 4.排出液排放标准:达到三类海水水质标准 与本项目相关的综合处理池出口液主要指标列于下表:(排放液水质优于该指标)排出液主要指标 COD 悬浮物 Pb* As* pH 4.0mg/L 11mg/L 0.049μg/L 4.2μg/L 6.5 * 表中所列重金属值与海水本底相近,即脱硫过程中几无重金属增加。三、治理成果 :每年排放碱性白泥(干料)约12万吨,是污染胶州湾的公害,青岛发电厂与黄岛发电厂每年排放二氧化硫约12万吨,是污染青岛大气的公害,两者长期难以解决。为恢复青岛碧海蓝天的生态环境和旅游景观,白泥与二氧化硫必须治理。 1997年他们提出用碱厂白泥脱除二氧化硫的双向治理方案后,得到市科委认可并立项研究。先后在青岛碱厂完成1000Nm3/h烟气处理量的海水—白泥/盐泥乳脱硫中试;在青岛发电厂完成3000Nm3/h烟气处理量的海水—白泥乳脱硫工业性中试;在黄岛发电厂完成10000Nm3/h烟气处理量的海水—白泥/废灰乳脱硫工业性中试,同时结合中试完成了大量实验研究工作。 该项目的技术路线是以海水为介质,添加0.1~0.5%白泥作为脱硫液,经吸收塔吸收二氧化硫后进入综合处理池,流出液再与二次海水混合,达标排放。 中试结果表明:吸收1公斤二氧化硫可以溶耗约1.8公斤白泥;脱硫海水中加入0.1%白泥后吸收能力提高约10倍;脱硫后白泥基本溶解;除硫酸根及钙离子稍有增加外,水质与原海水相近。 该项目的创新点是用白泥脱除二氧化硫,以废治废,双向治理;在相关化学反应及其动力过程深入研究的基础上,优化了反应过程,并合理利用了系统中存在的催化剂和絮凝剂,提高了脱硫效率;综合处理池设计新颖、性能优异,具有反应、中和、曝气氧化及分离澄清等综合作用;该技术利用白泥作助剂,其脱硫效率、曝气氧化、适用煤种及运行费用优于单纯海水脱硫法,具有国际先进水平。 为避免白泥脱硫后海水外排可能对附近海区产生不良影响,建议采用0.3~0.5%白泥的海水作为脱硫液,烟气/海水(V/V)比值取1000~1500,此时脱硫率为91%~96%,对应一台300MW发电机组的脱硫液用量为750~1200m3/h。由于脱硫后白泥溶解,流出液可替代海水用作冲灰水,然后随大量粉煤灰进入郊外的大灰场,在漫长的停留时间里进行自然净化。“白泥脱硫、双向治理”可考虑作为青岛发电厂海水脱硫的后备方案。 除白泥外,其它碱性废物(如废灰、电石泥、石灰石、镁盐等)也可用作海水脱硫助剂。利用黄岛发电厂半干法脱硫废灰作为助剂所做的中试已获成功,并申请在215MW机组上采用。 本项目成果适用于沿海地区,特别是氨碱法纯碱厂自备电厂与生产锅炉,以及附近电厂的烟气脱硫。具有设备投资少,运行费用低,适应煤种广,无二次污染,以及废物利用、双向治理等特点。
半干法烟气净化系统是将干法、湿法二者的优点集为一体,提出喷雾干燥净化法(半干法) 设计了喷雾干燥净化塔,喷雾干燥净化塔的净化过程是将烟气从高温冷却到低温,并喷入碱性料浆使之与烟气中的酸性气体反应且同时得到干燥的盐类产品,再用布袋除尘器加以回收。也即将水、碱性溶液或某些盐类溶液雾化成很细的雾滴与烟气中的酸性气体进行充分的传质传热,不但提高了效率,同时也可以使反应生成物得到干燥,最终得到易处理的干粉状生成物。
工作原理:
从玻璃池窑尾部排出的含酸性物质的烟气被引入净化塔底部,在这里与水、石灰乳和还具有反应性的循环干燥副产品相混合。在净化塔内的干燥过程中,石灰乳被高速的烟气吹散,石灰和烟气中的酸性组分充分接触,增大了石灰反应表面积,加速传质传热反应。由于高浓度的干燥循环物料的强烈紊流和适当的温度,使石灰乳被最有效地吸收和中和。
含有废物颗粒、残留石灰和飞灰的固体物在净化塔后的旋风分离器内分离并返回净化塔。由于固体物的循环流动,使循环中的石灰未反应部分再度与烟气中的酸性物反应,通过固体物循环使石灰的利用率提高到最大值,降低运行成本。反应完全的废物颗粒从净化塔底部排出。
喷射的石灰乳与烟气中的酸性气体中和后的副产品在旋风分离器和净化塔间循环。因此,新鲜石灰乳与酸性烟气能保持较大的反应表面。
烟气净化塔的高度提供了恰当的化学中和反应和水份蒸发吸热所需的时间。
石灰乳通过浆泵泵入净化塔内的雾化喷头。石灰乳喷入量满足净化烟气排放要求。
通过可调节水量的另一喷头将水喷入净化塔,以维持烟气净化中所需的温度,该温度必须尽可能低,因为烟气中吸收酸性成分的能力是随温度的降低而增加。但太低的温度将增强净化塔中循环物的粘结趋势。兼顾这两种趋势,将温度控制在120~140℃。
雾化喷头是一种由压缩空气雾化液体的六孔双流体型喷头,采用硬质合金材料,坚固耐磨。易于维护,可以在不停机的情况下快速更换。为防止喷头堵塞,在石灰乳制备装置中设有80目的液体过滤振动筛。
去除酸性气体后的烟气通过旋风分离器顶部进入布袋除尘器,除去粉尘和灰粒,净化后满足要求的的烟气通过烟囱排入大气。
其它方法 包括活性炭吸附法、氧化镁法等,技术较成熟,脱硫效率变化较大。
至今为止,世界上已有2500多套FGD装置,总能力已达200,000MW(以电厂的发电能力计),处理烟气量700Mm3/h,一年可脱二氧化硫近10MT,这些装置的90%在美国、日本和德国。
尽管各国开发的FGD方法很多,但真正进行工业应用的方法仅是有限的十几种。其中湿式洗涤法(含抛弃法及石膏法)占主导地位。
尽管各国在FGD方面都取得了很大的进步,但各种方法均有各自的局限性,因此,至今许多研究者仍在不断研究开发更先进、更经济有效的FGD技术。
脱硫工艺选择比较
脱硫工艺方案比较表
|
普通石灰石-石膏工艺 |
喷雾干燥法 |
炉内喷钙+尾部增湿 |
氧化镁法 |
旋流板塔湿式吸收法 |
技术成熟程度 |
成熟 |
成熟 |
成熟 |
成熟 |
成熟 |
适用煤种 |
不限 |
中低硫煤 |
中低硫煤 |
中低硫煤 |
不限 |
单机应用经济性规模 |
200MW及以上 |
100MW及以下 |
200MW及以下 |
200MW及以下 |
200MW及以下 |
脱硫率 |
95%以上 |
75-80% |
75-80% |
90%以上 |
75-90% |
吸收剂 |
石灰石/石灰 |
石灰 |
石灰石 |
氧化镁 |
石灰/碱液/电石渣等 |
吸收剂利用率 |
90%以上 |
50-70% |
约40% |
90%以上 |
85%以上 |
副产物 |
石膏 |
亚硫酸钙 |
亚硫酸钙 |
硫酸镁 |
亚硫酸钙/硫酸钠等 |
副产物处置 |
利用 |
抛弃 |
抛弃 |
回收 |
抛弃 |
废水 |
有 |
无 |
无 |
有 |
少量 |
占地面积 |
大 |
中 |
小 |
中 |
中 |
市场占有率 |
高 |
一般 |
一般 |
低 |
一般(国内最高) |
国内应用 |
珞璜,北京,半山,重庆等 |
黄岛,白马 |
下关,钱清 |
无 |
多家 |
为更深入了解各种脱硫经济技术现状,现以浙江嘉兴锦江热电厂为例,旋流板塔烟气脱硫工艺与现有国外引进技术作一比较,见下表。
经济技术比较
脱硫工艺 |
用 户 |
产地(厂家) |
配套主机 |
脱硫效率 |
投 资 |
石灰石-石膏法 |
四川珞璜电厂 |
日本三菱重工 |
2×360MW |
95% |
620美元/kW |
简易石灰石-石膏法 |
太原第一热电厂 |
日本 |
300MW |
80% |
日本政府赠送 |
炉内喷钙 |
钱清热电厂 |
芬兰IVO公司 |
125MW |
65% |
360元/kW |
石灰石-石膏法 |
杭州半山电厂 |
德国 |
2×125MW |
95% |
1960元/kW |
旋流板塔双碱法 |
嘉兴锦江热电厂 |
浙江大学 |
2×25MW |
80% |
120元/kW |
第二篇
脱硫系统防腐工艺介绍(湿法)
气脱硫,即对燃煤产生的SO2 烟气通过化学置换反应进行吸收和洗涤,降低烟气中SO2的含量,从而达到降低烟气排放后由于SO2对大气的污染的目的。
脱硫系统示意图
脱硫系统的主要设备构成:
² 吸收塔
吸收塔是整个脱硫系统中最为关键的设备——整个的脱硫工艺(脱硫过程)均是在吸收塔内发生!
² 烟道
烟道串联整个的脱硫系统,是烟气的运输通道。
² 烟气换热器-GGH
烟气换热器简称GGH。在不使用冷却塔的脱硫系统中,它是烟气能否进行排放的关键设备!
² 事故浆液罐
事故浆液罐是整个脱硫系统的备用贮罐!在吸收塔停止工作时,吸收塔内的剩余浆液全部排放至事故浆液罐内进行贮存。
² 石灰石浆液罐
石灰石浆液罐负责向吸收塔提供用于进行置换反应的石灰石浆液。
² 石膏溢流浆罐
石膏浆液罐用于将吸收塔内已经完成置换反应后产生的石膏浆的临时存放。
² 其它设备
其它设备是指根据不同的脱硫工艺和电厂实际情况而配套的相关贮罐。例如:1级/2级浆液循环箱、废水出水箱、中和/沉淀/絮凝箱、工艺水箱,等等。
吸收塔
收塔是整个脱硫系统中最为关键的设备——整个的脱硫工艺(脱硫过程)均是在吸收塔内发生!
功能:原烟气经由入口由下至上流动到烟气出口(根据热气上升的原理+增压风机的作用),在这一上升的过程中经过喷淋层和除雾器。在经过喷淋层的时候与喷淋管喷出的浆液混合,进而发生化学的置换反应,将原烟气中的硫离子置换出来形成硫酸钙,从而达到‘脱硫’的目的;在经过除雾器的时候,除雾器将烟气中蕴含的大量水分进行吸除,最后烟气进入吸收塔出口排出吸收塔!
工艺:烟气进入吸收塔后向顶部流动,并与自上而下流动的、含有吸收剂的浆液接触。吸收剂借助循环泵通过循环管道和喷淋管束进入吸收塔的上部,并在重力作用下洒落到吸收塔的下部。在添加新石灰石后,石灰石、副产品和水的混合物通过吸收塔再循环管重新循环流到喷淋层。这种浆液通过喷嘴雾化成细小的液滴。这些细小的液滴在返回吸收塔浆池的整个过程中将会改善烟气中的酸性组分,如SO2、SO3、HCI及氯离子等。在吸收塔中吸收SO2过程中烟气将被来自循环浆液中的水饱和到水饱和状态,并被冷却到绝热饱和温度。水损失由工艺水补充;并且,为了最有效的利用吸收塔的水,用来清洗吸收塔顶部的除雾器的工艺水将用作补充水。在喷淋层上方装设有二级除雾器,以便除去大量仍然残留的液态小滴。由除雾器排出的分离物将返回吸收塔中。吸收塔基本分为三个区段:A,吸收区。在本区段内一些酸性成分,主要是SO2和SO3将被吸收并溶解于浆液的水中,随后再与石灰石反应变成石膏。B,再循环浆池。用途是:氧化亚硫酸,使其生成硫酸根;溶解新石灰石;使硫酸盐与溶解的石灰石反应生成石膏;石膏结晶。C,气区。在吸收塔的上部烟气直接通过两级水平安装的除雾器,以便于使小雾滴减少到最低限度。清洗除雾器的冲洗程序是按吸收塔的需水量来计算的。
吸收塔内有许多的配套的工艺系统,现就其中的主要部件进行说明(与吸收塔相关的工艺管接口参见其它的设备说明,在此不作描述):
Ø 原烟气入口
原烟气入口是指由GGH一次出口经由烟道而进入吸收塔的、在吸收塔本体上的烟气进口。其安装角度与吸收塔中轴线大约呈15º角。
根据设计的不同(主要指其材质),原烟气入口有防腐和不需防腐两种情况:
防 腐——当原烟气入口的材质选用普通碳钢时,因为普通碳钢不耐腐蚀,故而需要在碳钢表面设置防腐层加以保护!其防腐方案的考虑:在整个原烟气入口进行整体的玻璃鳞片涂刷;此外,在业主特别要求的情况下,考虑到以后的生产中需要使用铲、凿用以去除玻璃鳞片表面积留的石膏凝结物,为加强对防腐层的保护,艾柯尔橡胶防腐有限公司的英国专家在欧洲的很多脱硫项目上根据工况条件特别在玻璃鳞片表层铺设一层耐酸瓷砖。耐酸瓷砖的铺设原则是:整个原烟气入口底部,以及两个侧面高约500mm的区域。
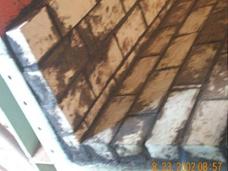
底部衬砖(涂层表面) 底部及角部衬砖(涂层表面)
注意:如果需要加衬耐酸瓷砖进行防腐保护的话,由于考虑到瓷砖贴衬后在生产中的温度变化而导致瓷砖的起拱变形,因此必须在进行防腐施工以前,在原烟气入口底部焊接地笼(规格大约为1000mm*1000mm)用以在以后的耐酸瓷砖贴衬的加固!
不防腐——当原烟气入口的材质选用合金钢时,原烟气入口就不再需要进行防腐保护!
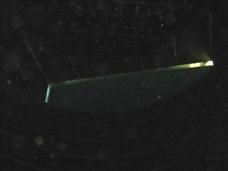
吸收塔出口 吸收塔入口
Ø 净烟气出口
在吸收塔内经过净化了的烟气穿过除雾器后从位于吸收塔顶部的净烟气出口排出。在净烟气出口处,平均分布有3根立柱。
Ø 除雾器安装层
除雾器安装层的结构较为复杂,共分2个部分:一是同一截面上平均分布的3根横梁;二是在吸收塔塔壁四周安设有一圈平台,平台上表面与横梁上表面水平。除雾器本体就安装在横梁与支座上面。
除雾器横梁衬胶(IQL-190-4mm) 除雾器周圈支座衬胶(IQL-190-4mm)
Ø 喷淋层
在原烟气入口的上方约1M高处,设置有喷淋层。喷淋层共设有上、中、下3层,每层的结构形式一致,唯一的区别就是每一层喷淋层的角度有偏差。每层喷淋层均由2部分组成,一是喷淋层横梁;二是安装在吸收塔壁上的11个支座,支座的安装角度共有3种。
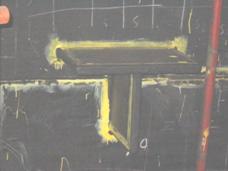
喷淋层交叉梁衬胶(IQL-190-4mm) 喷淋层支座衬胶(IQL-190-4mm)

喷淋层支座衬胶(IQL-190-4mm) 喷淋层支座衬胶(IQL-190-4mm)
Ø 氧化空气管
在原烟气入口的下方,吸收塔内积有高度约9~10M的浆液,在这些积液中通有氧化空气管,生产过程中,氧化空气通入积液用以加速浆液中的化学反应。氧化空气管共分为3段:一段在吸收塔内,外端与吸收塔上的法兰连接,材质为玻璃钢(FRP);第二段在吸收塔外,与在吸收塔外法兰连接的玻璃钢管道的法兰相连接(以上两段管道的连接方式参见后附上的该区域的衬胶图纸),此段的材质一般采用合金钢,安装形式为倒转90º的‘Z’字形,用以防止浆液的倒灌而腐蚀钢管;第三段管道与第二段相连接,在吸收塔外呈水平布置,材质为普通的碳钢。
作用:借助氧化空气管并通过搅拌器前面的喷枪将氧化空气输送到吸收塔的集液区,这样使氧化空气很好地分配于浆液中。同时氧化空气鼓送到中集液区,以便将亚硫酸钙氧化成硫酸钙。
氧化空气管全部都不需要进行防腐——玻璃钢管道是设备采购部件,其它两段为现场安装部件。在进行工期安排时,该部分的安装排在喷淋层(管)安装完毕后,吸收塔脚手架拆除期间穿插进行。
Ø 浆液搅拌器
在由吸收塔底部起向上高度约为1.5M和6M处,分别安设有搅拌器。具体布置为:6M高处设有2个搅拌器,呈180º对称布置;1.5M高处设有3个搅拌器,呈120º布置。搅拌器的搅拌轴的轴线均向下倾斜,角度约为15º。
一般情况下,搅拌器的安装时间安排在脚手架拆除完毕、吸收塔底部衬胶完成后进行。但是,如果安排在底部衬胶前进行的话,就必须考虑到在进行喷砂时,对1.5M处设置的搅拌器加以防护——防止对搅拌器(不锈钢制)表面的破坏。
由于搅拌器的搅拌作用,致使整个吸收塔内的浆液在整体上呈缓慢的顺时针旋转。
Ø 循环浆液管口
在吸收塔的底部,设有3个直径约为∮900mm的浆液管孔,孔中心线呈平行布置。在吸收塔内壁、浆液管孔的四周,竖向两排(每排3个)对称布置了共6个安装用的挂桩,用于挂设浆液管滤网(滤网和挂桩的材质均为合金钢)。
挂设滤网的目的是防止较大的石膏浆块进入循环浆液泵内,进而损伤循环浆液泵。
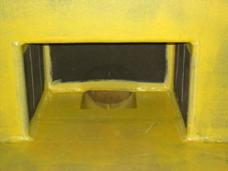
循环浆液管口衬胶(IQL-190-4mm) 排空箱衬胶(IQL-190-4mm)
Ø 排空箱
排空箱设置在吸收塔底部,具体结构形式参见后附的衬胶图纸。其作用是在脱硫系统停机时用以排出吸收塔底部积留的石膏浆。吸收塔外部设置有排浆液的沟道(一般采用玻璃钢或衬砖进行防腐)承接排空箱排出的石膏浆。
烟 道
道串联整个的脱硫系统,是烟气的运输通道。根据烟道内运行烟气的物理状态以及所处的位置不同,烟道共分5节:第一节——由除尘器至增压风机,热态的、没有太大压力的原烟气;第二节——由增压风机至烟气换热器入口的,有一定压力的、热态的原烟气;第三节——由烟气换热器出口至吸收塔原烟气入口的,温度相对降低的原烟气;第四节——由吸收塔净烟气出口至GGH再热入口的,冷态的净烟气;第五节——由GGH再热出口至烟囱的,热态的净烟气。——由于各个FGD系统的设计方或者是承包方的不同,以上五节烟道的数字编号也不相同。
Ø 第一节——由除尘器至增压风机,热态的、没有太大压力的原烟气
当烟气经过除尘器以后,烟气中混合的大量的灰尘被祛除。通过在除尘器后设置的负压抽风机将烟气排出至增压风机。
Ø 第二节——由增压风机至烟气换热器入口的,有一定压力的、热态的原烟气
通过增压风机,对原烟气气流进行加压送至GGH入口。此时的原烟气温度约为:正常140~160℃,瞬时180℃(持续时间≤30min)。
该段烟道的防腐区域仅为末端的2节(以排水沟为界限)。均采用IQLC802B耐高温玻璃鳞片进行防腐。
Ø 第三节——由烟气换热器出口至吸收塔原烟气入口的,温度相对降低的原烟 气
经过GGH的降温后,烟气的温度由140~160℃降低至110℃左右。由于该段烟道内的温度超过了橡胶板所能够承受的界定值,因此与第二段的防腐方式一样——采用IQLC802B高温玻璃鳞片进行防腐。
Ø 第四节——由吸收塔净烟气出口至GGH再热入口的,冷态的净烟气
烟气在吸收塔内经过脱硫处理后,由于浆液的降温作用,所以此时的烟气为净烟气,温度为40~70℃。这段烟道由于烟气的温度较低,故而可以采用IQL-190-4mm衬胶或IQLC802A标准型玻璃鳞片两种方式进行防腐。
Ø 第五节——由GGH再热出口至烟囱的,热态的净烟气。
经过GGH的加温,烟气的温度由40~70℃升至100℃左右。热烟气本身的自然上升+烟囱因为高度而产生的负压作用,由GGH再热出口出来的热烟气通过烟囱排放到大气中。该段烟道同样采用IQLC802A标准型玻璃鳞片进行防腐。
注意:在第二节、第三节、第五节烟道内的弯头处,均设置有导流板,对所通过的烟气起到导向的作用!
烟气换热器
烟气换热器,又称GGH(Gas-Gas Heat)。
在脱硫系统中,当设置有专用的冷却塔时,可以省略GGH!
GGH是一台结构极为复杂设备,分为原烟气侧和净烟气侧两个部分,而原烟气侧和净烟气侧又各再分为上下两个区——热态区和冷态区。原烟气侧和净烟气侧以位于GGH正中央的中间梁(上、下各一)为界限。在GGH的中央布置有中心筒体,中心转轴就安设在中心筒体内部。在中心筒体外壁,安装着转子隔仓,转子隔仓内放置换热元件。
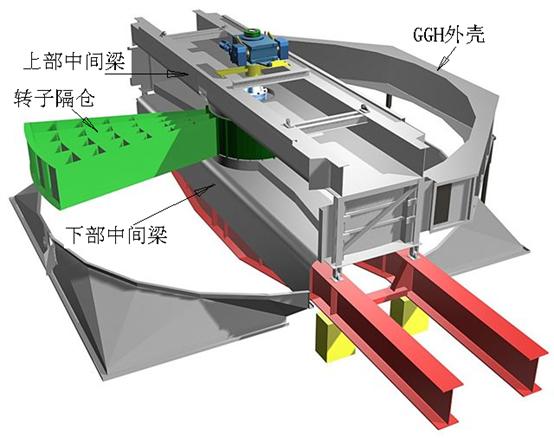
在GGH内部,根据其本身的结构和工艺,还设置有相关的附件。
其中最主要的还有:1、气密封结构。气密封结构有两种——A、径向密封。径向密封的密封面设置在上部中间梁的下表面处,密封片安装在转子隔仓上面(两个转子隔仓夹住一片密封片)。当转子旋转时,密封片随转子转至中间梁处,此时控制密封片与密封面之间的间隙,同时由GGH外部的空气管道向位于下部中间梁上的气密封板通入带压空气,直至上部的中间梁以达到隔绝净烟气侧和原烟气侧,防止两边的烟气串流的目的。B、环形密封。环形密封设置在转子外壳内侧的表面上的上下两处的钢性环处。以转子的外圆周作为密封面,安装在钢性环上的密封片靠在转子外圆周上,以此隔绝热态区和冷态区,防止烟气回流。2、拉杆结构。由于GGH的直径较大(约11M),为保持其外壳结构上的钢度,故必须在外壳与中心筒体间设置拉杆。
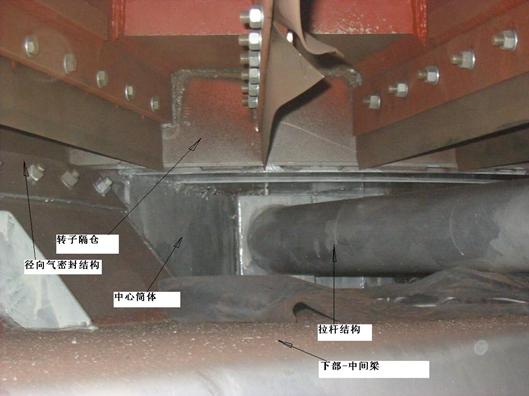
功能:当原烟气由第二段烟道进入GGH烟气一次入口后,穿过正在以慢速旋转的转子,在通过转子隔仓内安装的换热元件后,原烟气的温度被换热元件吸走,原烟气的温度由140~160℃降低至110℃左右,而换热元件所吸去的热量通过转子的旋转将之带到另外一侧——净烟气侧。温度降低后的原烟气从一次出口通过第三段烟道进入吸收塔脱硫。
当在吸收塔内脱硫以后的净烟气由第四段烟道进入GGH再热入口以后,再通过由在原烟气侧吸附了热量、并旋转至净烟气侧的换热元件以后,净烟气的温度由40~70℃升至100℃左右。升温后的净烟气通过第五段烟道至烟囱,最终向大气中排放。
整个GGH内部均采用IQLC802B耐高温玻璃鳞片进行防腐。
石灰石浆液罐/石膏浆液罐/事故浆液罐
石灰石浆液罐/石膏浆液罐,两种贮罐的内部结构相似,均设置有阻流板和搅拌器。在贮罐的内侧墙壁上,安设有2~3组阻流板,防止在当搅拌器进行持续搅拌时,罐内浆液与搅拌器的旋转速度形成共振,同时也降低浆液的旋转速度。
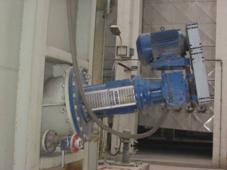
阻流板的设置(IQL-190-4mm) 事故浆液罐-搅拌器安装
在贮罐的顶壁中央,开设有一个法兰孔,孔外部设置有一个立式搅拌器,用以充分混合贮罐内的浆液,防止浆液沉淀结块。
贮罐内部均采用衬胶以进行防腐。
事故浆液罐是整个脱硫系统的备用贮罐!在吸收塔停止工作时,吸收塔内的剩余浆液全部排放至事故浆液罐内进行贮存,在事故浆液罐壁部距底部约1M高处,水平圆周上平均布置了三台带有安装倾角的搅拌器,用以对内存的浆液进行充分地搅拌,防止浆液凝结成块状物!